COPPER BERYLLIUM
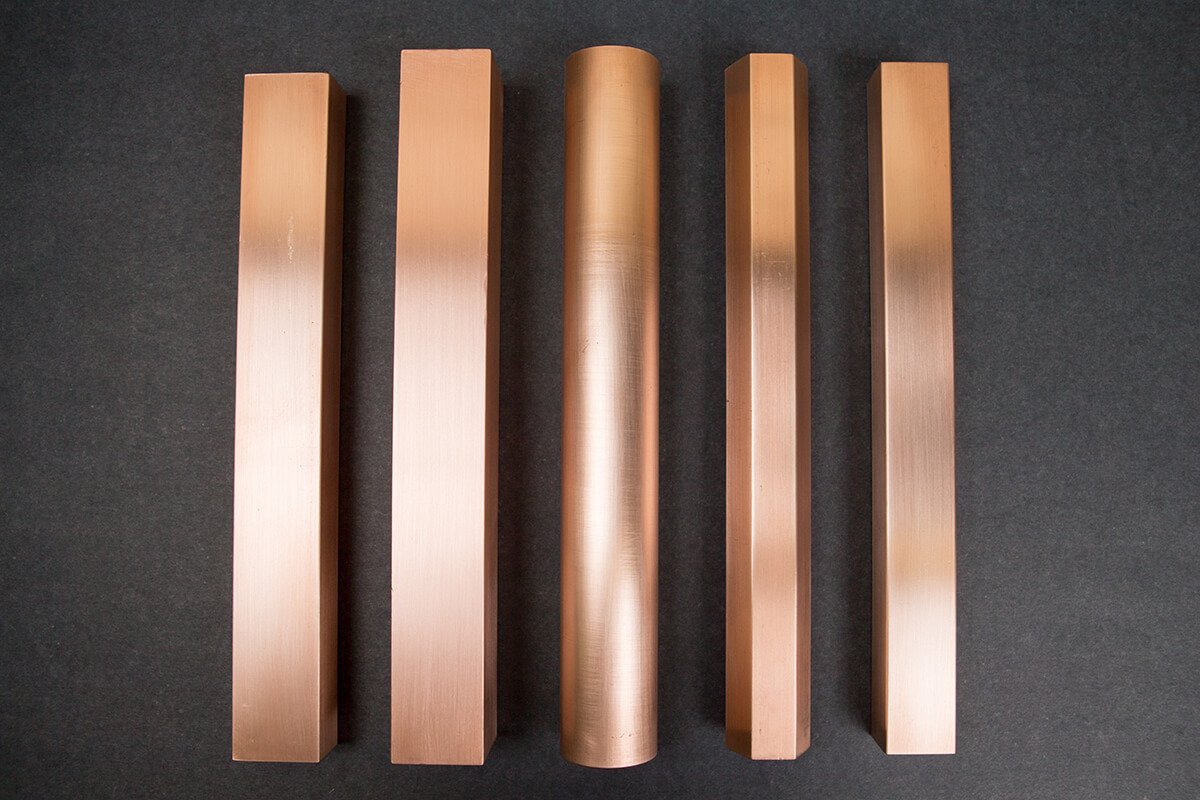


Copper Beryllium C17200, RWMA Class 4
Other Designations: AWS J1.3, ASTM B196, AMS 4533, SAE J461, CuBe2.1247, Alloy 25, Mold-Mor® 3, Mold-Mor® 4
Copper Beryllium is the highest strength copper alloy and is specified when the mechanical strength is the limiting design feature for a copper alloy. It is a heat treatable copper alloy having the unusual combination of very high hardness and strength and lower electrical conductivity than AWS J1.3/ RWMA Class 3 materials. Specify Cadi MOLD-MOR® 3 or 4 for mold applications.
Chemical Compositions of RWMA Materials Group A - Copper Base Alloys |
||||
RWMA Class |
UNS Number |
Description |
Cu |
Be |
4 |
C17200 |
Beryllium Copper |
Balance |
0.02% max. |
Cu: Copper
Be: Beryllium
Typical usages of C172 RWMA Class 4 copper alloy: C17200 is recommended for flash and upset welding dies, projection welding and seam welding bushings, and other applications requiring harder copper alloys.
Fabrication Properties of C17200 Alloy:
- Machining - C17200 copper alloy has a machinability rate of 20%.
- Welding - Butt welding, seam welding, spot welding, coated metal arc welding, gas-shielded arc welding, brazing and soldering are recommended for C17200 copper alloys. Oxyacetylene welding is not recommended for C17200.
- Forging - For C17200 occurs at a temperature of 649 to 816 degrees Celsius.
- Hot working - C17200 copper alloys have good hot working capabilities.
- Cold working - C17200 copper alloys have excellent cold working properties.
- Annealing - Is the process of heating metal or glass and allowing it to cool slowly. This process removes internal stresses and strengthens it. C17200 copper alloys are annealed at temperatures from 774 to 802 degrees Celsius
Other fabrication properties include drawing, drilling, blanking, forming and bending, tapping, and turning.
GENERAL USES OF C17200 |
|
||
Back-up Electrodes |
Bushings |
Caps & Shanks |
Casting Wheels & Dam Blocks |
Continuous Casting Molds |
Cross Wire Welding Electrodes & Components |
Dies & Fixtures |
Electrode Holders and Adaptors |
Electrical & Mechanical Power Components |
Flash & Butt Welding Dies |
Injection Blow Molds & Dies |
Joining Components |
Nut & Stud Welding Electrodes |
Permanent Molds |
Pistons |
Plunger Tips |
Resistance Welding Electrodes |
Seam Weld Wheels |
Shafts |
Spot Welding Electrodes |
Threaded Electrodes |
Wear Plates |
Welding Arms |
Welding Blocks |
Welding Connectors |
Welding Platens |
|
|
Item Name: | Copper Beryllium Alloy C17200, ASTM B196 |
RWMA (Resistance Welding Manufacturing Alliance) Class: | Class 4 |
Principal Element: | Cu, Be |
Minimum Hardness Rockwell (up to 1" dia.): | HRC 33 |
Minimum Electrical Conductivity (% IACS): | 20 |
Metal Stock Availability: | Stocked in mill form or precision cut to your specifications. |
Shape: | Bar Hexagon Octagon Plate Rectangle Round Special Square |
Length for Round, Hexagon, Square, Octagon, Rectangle, Special Shapes: | All sizes in standard lengths up to 12 ft Special Sizes |
Diameter for Round, Hexagon, Square, Octagon, Rectangle, Special Shapes: | 1/8 to 8 in Special Sizes |
Thickness for Plate: | 1/2 to 10 in Special Sizes |
Quality Assurance
Quality Policy: Cadi Company Inc. is dedicated to world-class excellence. Our commitment is to continually achieve the highest standards required to meet our customer’s needs. Cadi is committed to a policy of continuous improvement within all areas of the organization through customer communication, by means of quality planning and review, as well as employee training and participation to achieve the Cadi commitment goal of 100% in quality, effectiveness, and customer satisfaction.
Quality Objectives: Cadi Company, Inc. is committed to the development and implementation of the ISO Quality Management System. We pledge that through the efforts of all our employees working together as a team, we will continually strive to be a leader (in our markets) in satisfying our customers’ needs with regard to service, performance, and competitive pricing. Cadi shall maintain global and domestic sources to provide quality products as required by our customers. Cadi will provide our customers with the highest level of satisfaction by achieving the goal of 100% in the areas of product quality and on-time delivery performance.
Cadi Company is committed to providing goods and services that meet or exceed our customer’s requirements and expectations. It is our firm belief that this dedication to the highest standards is the cornerstone of our existence.
- We have the equipment and processes to guarantee the quality of the products we manufacture.
- We continually upgrade our equipment and have ongoing training company-wide.
- Each order undergoes stringent Quality Assurance Processes to assure accuracy and precision to the client’s specifications and is verified throughout the manufacturing cycle with scheduled quality assurance audits.
- All material is subject to detailed physical tests where microstructures, tensile, yield strength, U.T. testing, eddy current conductivity, elongation, and hardness are measured and reported.
- Climate-controlled inspection facility.
- We have a Metallurgical Engineer on-site for any technical questions.
To ensure Cadi follows rigorous quality and procedural protocols we are ISO 9001:2015 Certified and have been for over 18 years.
ISO Certification: | 9001:2015 (Registration # 10002745 QM15 Valid until 2027-08-21) |
Reports: | Certification of Compliance Chemical Analysis Final Inspection Material Test Reports |
Mechanical and Physical Testing: | Elongation Grain Size Hardness Tensile Yield |
Nondestructive Testing: | Chemical Analysis Conductivity Liquid Penetrant Ultrasonic X-Ray |
Alloy Applications Cross Reference Chart | C15000 | C18150 | C18000 | C18200 | C17510 | C17200 | C15760 |
Axial Conductors | X | - | - | - | - | - | - |
Back-up Electrodes | X | X | X | X | X | X | X |
Bushings | X | X | X | X | X | - | - |
Caps & Shank | X | X | X | X | X | X | X |
Casting Wheels | X | X | - | X | - | - | - |
Casting Wheels and Dam Blocks | - | - | X | - | X | X | - |
Centrifugal Casting Mold | X | X | X | X | - | - | - |
Circuit Breaker Parts | X | X | - | X | - | - | X |
Collector Connector | X | X | - | X | - | - | - |
Collector Housing | X | X | - | X | - | - | - |
Connector Bar | X | X | - | X | - | - | - |
Connectors | X | X | X | X | X | - | X |
Connection Lead Bar | X | X | - | X | - | - | - |
Continuous Casting Molds | X | X | X | X | X | X | - |
Cross Wire Welding Electrodes & Components | X | X | X | X | X | X | X |
Damper Ring/Finger | X | X | X | X | - | - | - |
Dies & Fixtures | X | X | X | X | X | X | - |
Die Casting Pistons | - | - | X | - | X | X | - |
Die Casting Plunger Tips | - | - | X | - | X | X | - |
Electrode Holders & Adaptors | X | X | X | X | X | X | - |
Electrical & Mechanical Power Components | X | X | X | X | X | X | X |
Flash & Butt Welding Dies | X | X | X | X | X | X | X |
Flexible Connector | X | X | - | X | - | - | - |
Heat Flux Components | X | X | X | X | X | - | X |
Injection Blow Molds & Dies | - | X | X | X | X | X | - |
Joining Components | X | - | X | - | X | X | X |
Lead Conductor Bar | X | X | - | X | - | - | - |
Motor End Rings | X | X | X | X | X | - | - |
Neutral Bus Bar | X | X | - | X | - | - | - |
Non-Sparking Applications | - | X | X | X | X | X | - |
Nut & Stud Welding Electrodes | X | X | X | X | X | X | - |
Performance Engine Components | - | - | X | - | X | X | - |
Permanent Molds | - | - | X | - | X | X | X |
Power Generation Products | X | X | X | X | - | - | - |
Power Semiconductor Bases | X | X | - | X | - | - | - |
Resistance Welding Electrodes | X | X | X | X | X | X | - |
Rotor Coil Bar | X | X | - | X | - | - | - |
Seam Weld Wheels | X | X | X | X | X | X | - |
Series Loop Segment | X | X | - | X | - | - | - |
Shafts | X | X | X | X | X | X | - |
Slip Rings | X | X | - | X | - | - | - |
Slot Wedge | X | X | X | X | - | - | - |
Snap Rings | X | X | - | X | - | - | - |
Special Nipple | X | X | - | X | - | - | - |
Sputtering Target Backing Plate | X | X | X | ||||
Terminal Box Connectors | X | X | - | X | - | - | - |
Threaded Electrodes | X | X | X | X | X | X | - |
Transmission Devices | X | X | - | X | - | - | X |
Water Clip | X | X | - | X | - | - | - |
Wear Plates | - | - | - | - | - | X | - |
Welding Arms | X | X | X | X | X | X | - |
Welding Blocks | X | - | X | - | X | X | - |
Welding Connectors | X | X | X | X | X | X | - |
Welding Platens | X | X | X | X | X | X | - |
Other References for C17200: RWMA Class 4 Copper, Class 4 Copper Alloy, Alloy 25, Beryllium Copper Rod, CuBe Copper, Beryllium Copper Suppliers, AMS 4533, ASTM C194, ASTM B196, CuBe Alloy, Alloy 25 Beryllium Copper, UNS C17200 and CDA C17200.