Sputtering Target Backing Plate
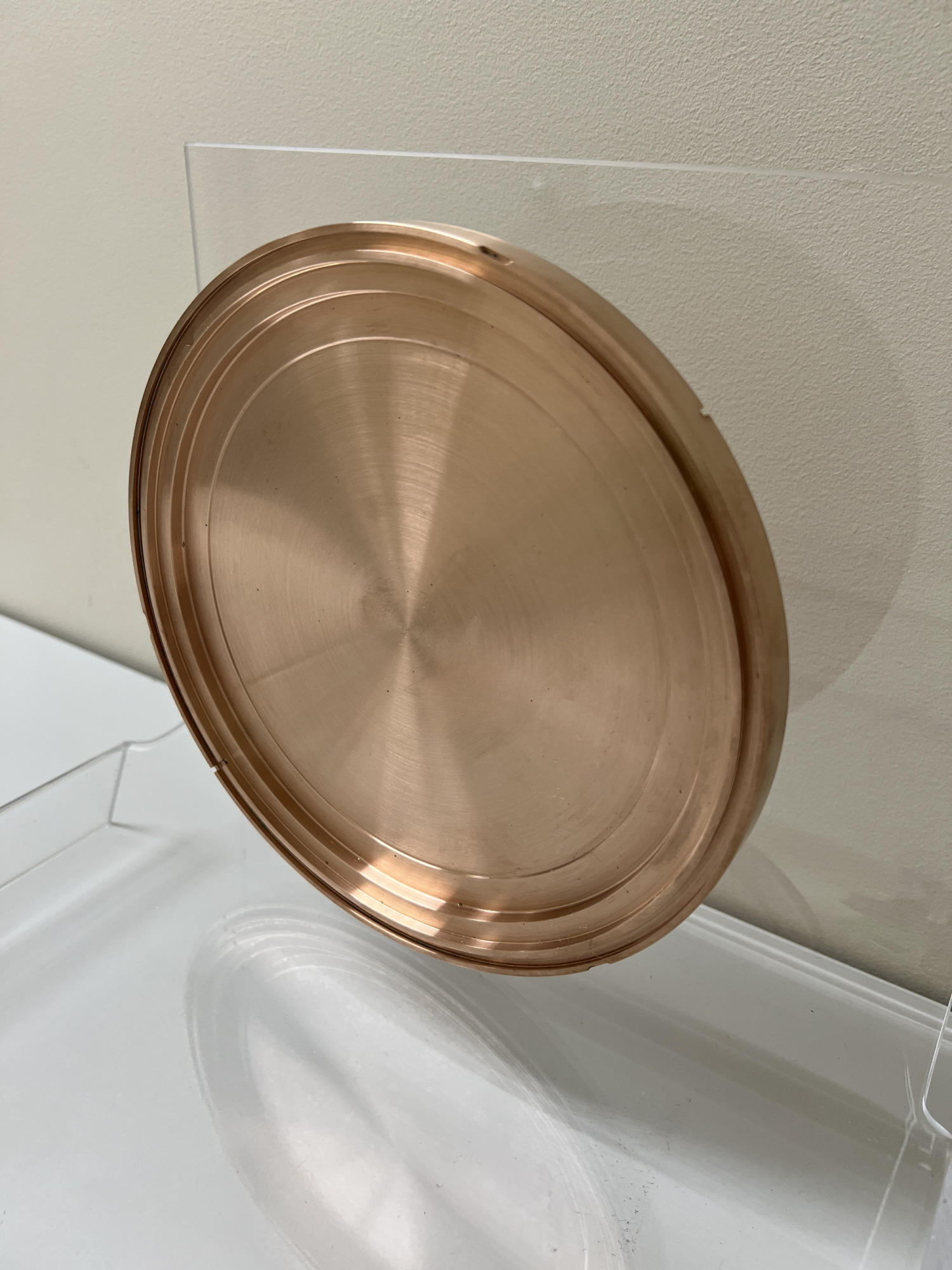


Copper Alloy Sputtering Target Backing Plates
(Blanks or Finished) out of:
C18150 Copper Chrome Zirconium, C17510 Copper Nickel Beryllium, and a Beryllium Free option C18000 Copper Nickel Silicon Chromium.
Copper alloy backing plates are an essential component in the field of sputtering of thin film depositions, particularly in the production of semiconductors and display devices.
These plates are typically manufactured from copper, copper alloy, stainless steel, molybdenum, or tungsten. The main purpose of these backing plates is to provide a stable support for the sputtering target material, ensuring uniformity and consistency during the sputtering process.
Copper alloys are often chosen as the ideal material because they offer high thermal conductivity with optimum mechanical stability. These copper alloy high conductivity backing plates aid in heat dissipation, preventing overheating issues that can affect the efficiency of sputtering systems.
Cadi Company, Inc., as a target supplier offers made-from-print custom targets made of high-quality copper alloys such as C18150 Copper Chrome Zirconium, C17510 Copper Nickel Beryllium, and a Beryllium Free option C18000 Copper Nickel Silicon Chromium.
Copper-Based Alloy |
|
Percentages |
Thermal Conductivity |
Electrical Conductivity |
Copper Chrome Zirconium (C18150) RWMA Class 2 |
Cu |
Balance |
187 Btu/sq ft/ft hr/ oF (TF00) |
75% IACS min. (TF00) |
Cr |
0.5 – 1.5 |
|||
Zr |
0.02- 0.20 |
|||
Copper Nickel Silicon Chrome (C18000) RWMA Class 3 Be Free |
Cu |
Balance |
(Precipitation Heat treated) 225 W/m*K , 130 BTU/hr. ft. F.
|
(Precipitation Heat treated) 45 % IACS min. (Solution Annealed) 18-22 % IACS |
Ni |
1.8 – 3.0 |
|||
Si |
0.4 – 0.8 |
|||
Cr |
0.1 – 0.8 |
|||
Copper Nickel Beryllium (C17510) RWMA Class 3 |
Cu |
Balance |
(Precipitation Heat treated) 225 W/m*K , 130 BTU/hr. ft. F.
|
Precipitation Heat treated) 45 % IACS min, 50% IACS typical (Solution Annealed) 40% IACS typical |
Ni |
1.4 – 2.2 |
|||
Be |
0.2 – 0.6 |