Injection Blow Mold & Thermo-Form Tooling (Mold - Mor®)
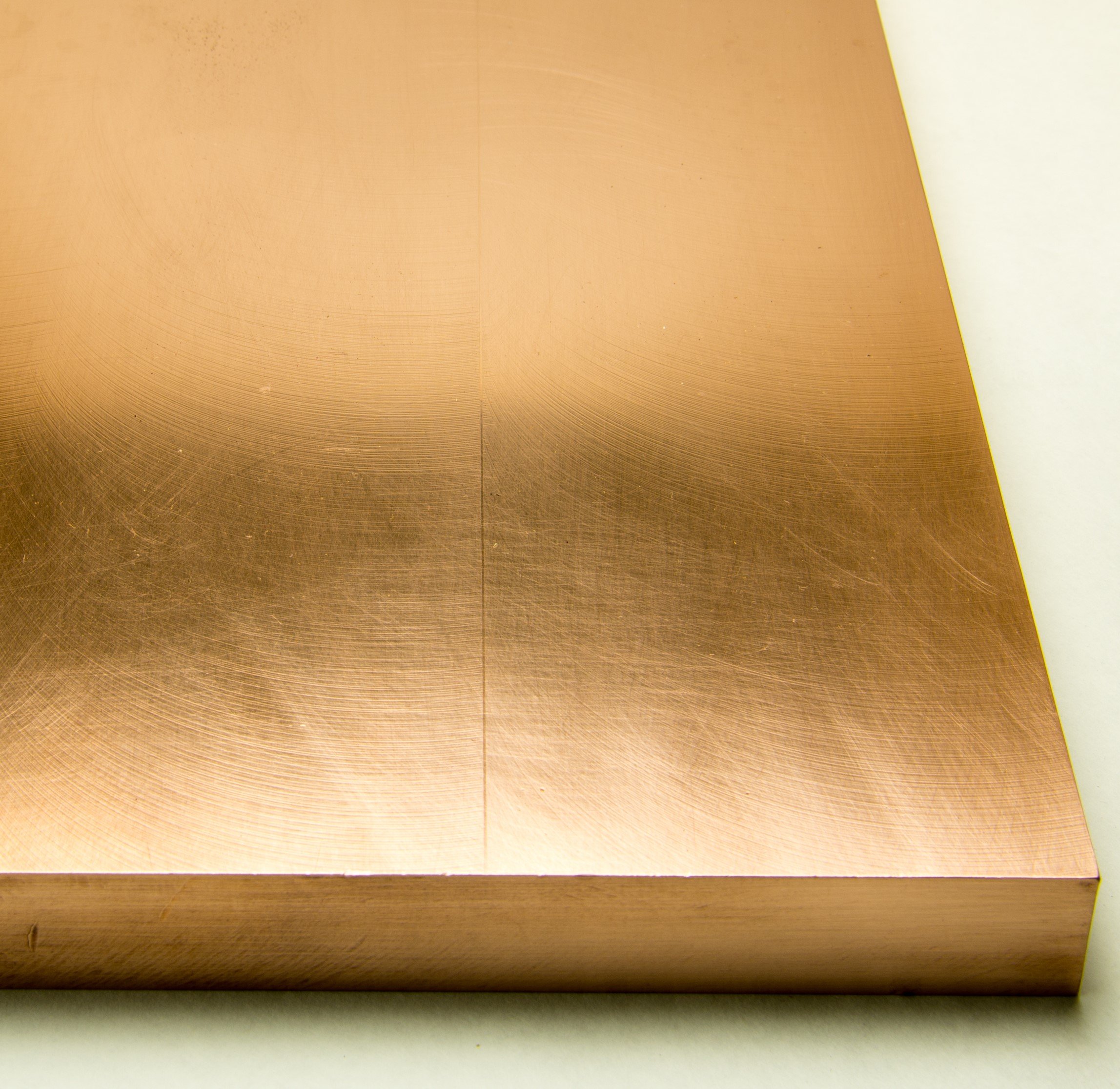


Mold Tools - Mold Mor
A System of Copper Alloys Offering the Optimum Combination of
Thermal Conductivity and Durability Required for Cost Effective Plastic Molding
MOLD-MOR® – 1 | (C18000) A Nickel Silicon Chromium Copper Alloy with high thermal conductivity (>135 Btu/Hr/Ft2/°F) and moderate hardness (RB95) |
MOLD-MOR® – 2 | (C17510) A Beryllium Copper Alloy with high thermal conductivity (>135 Btu/Hr/Ft2/°F) and moderate hardness (RB98) |
MOLD-MOR® – 3 | (C17200, 30C) A Beryllium Copper Alloy with good thermal conductivity (75 Btu/Hr/Ft2/°F) and high hardness (RC30) |
MOLD-MOR® – 4 | (C17200, 40C) A Beryllium Copper Alloy with moderate thermal conductivity (60 Btu/Hr/Ft2/°F) and very high hardness (RC40) |
MOLD–MOR® Features
- Exceptionally High Thermal Conductivity
- Excellent Tensile Strength Range
- Adequate Hardness Levels Without Addition Heat Treatments
- High Toughness Due to Ductility
- High Compressive Yield Strengths
- Easily Machinable to Good Finish
- Superior Corrosion Resistance
- Excellent Resistance to Wear, But Can Be Further Enhanced When Plated
- Nickel or Thin Dense Chrome Adheres Well
MOLD–MOR® Benefits
- Reduced Cooling Time
- Reduced Overall Cycle Time
- Increased Productivity
- More Even and Consistent Mold Surface Temperature
- Less Stresses in Molded Parts
- Reduced Dimensional Variation
- Less incidence of Sink Marks Form Hot Spots in Mold
- Improved Control for Warpage
- Easier Ejection Due to Cooler Surface Temperatures
- Greater Latitude in Coolant Channel Placement
MOLD–MOR® Applications
- Injection Mold Cores
- Injection Mold Core Pins
- Injection Mold Inserts
- Injection Mold Cavities
- Blow Mold Cavities
- Injection Mold Slides
- Injection Mold Chill Plates
- Injection Mold Runner Bars
- Injection Mold Sprue Bushing
- Injection Mold Sprue Puller Pins
- Blow Mold Neck Pinch Offs
- Blow Mold Tail Pinch Offs
- Blow Pins
- Thermo-Forming Cavities
- Rotational Molding Inserts
- Runnerless Molding Nozzle Tips
MOLD–MOR® Mold Design Tips
- Use when large amounts of heat must be extracted in short periods of time
- Install coolant circulating channels like conventional mold for maximum benefits when possible
- Utilize copper alloys in mold area where ideal coolant channel installation is not possible
- In small diameter multiple core pin applications, seat core pins on a chill plate
- In High wear applications, such as running glass filled materials, nickel or thin dense chrome plate alloy
- Apply zero preload on shut offs at parting lines and core pin shut offs due to ductility of the copper alloy (plastic will not flash with zero clearance at shut offs)
- Ensure good contact with mating surfaces to maximize cooling transfer
- Cap ends of cores when cooling is required at tip end and the hardness of steel is required on the seat end
- Extreme shut off areas can be welded with stainless steel to extend mold life
- Insert copper alloys in corners of mold cores to enhance cooling
- Insert mold areas when heavier wall sections are present on the plastic part
- Use when molding corrosive plastics
- Runner channels can be inserted with copper alloys so the runner does not dictate the molding cycle
- Use the right combination of properties to provide maximum performance in the mold
- MOLD-MOR 3 & 4, with its higher hardess levels, provides an excellent balance of hardness and high tensile strength
- MOLD-MOR 2, with its high thermal conductivity, works well when a high rate of heat must be transferred
- MOLD-MOR 1, offers an exceptional range of benefits and provides the fastest mold cycle and most consistent mold surface temperature
- MOLD-MOR 1, provides an exceptional good base for application of nickel and thin dense chrome plating
- Cadi copper alloys will solve your mold cooling challenges more economically
MOLD–MOR® Physical and Mechanical Property Comparison
Table 1 :
Mold Alloy | Thermal Conductivity (Btu/Hr/Ft2/°F) |
---|---|
MOLD-MOR 1 | 135 |
MOLD-MOR 2 | 135 |
MOLD-MOR 3 | 75 |
MOLD-MOR 4 | 60 |
P-20 | 17 |
H-13 | 15 |
420 SS | 13 |
ALUM QC7 | 93 |
Mold materials with high thermal conductivity provide maximum cooling benefits and faster molding cycles. Also, the higher the thermal conductivity numbers the faster the mold surface temperature will reach equilibrium, important for reducing stresses in the molded part. See table I for properties.
Table II :
Mold Alloy | Tensile Strength (ksi) |
---|---|
MOLD-MOR 1 | 100 |
MOLD-MOR 2 | 115 |
MOLD-MOR 3 | 170 |
MOLD-MOR 4 | 185 |
P-20 | 140 |
H-13 | 210 |
420 SS | 255 |
ALUM QC7 | 80 |
Tensile strength is extremely important in mold material selection. The Cadi copper alloys offer an exceptional combination of thermal conductivity and tensile strength. Tensile strengths are listed in Table II.
Table III :
Mold Alloy | Hardness |
---|---|
MOLD-MOR 1 | 95 Rb |
MOLD-MOR 2 | 98 Rb |
MOLD-MOR 3 | 30 Rc |
MOLD-MOR 4 | 40 Rc |
P-20 | 30 Rc |
H-13 | 45 Rc |
420 SS | 50 Rc |
ALUM QC7 | 91 Rb |
Cadi copper alloys have adequate hardness levels for applications when applied properly in mold designs. Toughness of a mold alloy is a combination of properties and not hardness alone. Hardness levels are listed in both the Rockwell B and C scale. See hardness comparisons listed in Table III.
Table IV :
Mold Alloy | Elongation (%) |
---|---|
MOLD-MOR 1 | 14 |
MOLD-MOR 2 | 14 |
MOLD-MOR 3 | 15 |
MOLD-MOR 4 | 7 |
P-20 | 20 |
H-13 | 15 |
420 SS | 10 |
ALUM QC7 | 7 |
A good combination of physical properties is important in selecting the proper mold alloy. An extremely hard material, with a low elongation value may crack or break easily. The combination of high ductility and excellent tensile strength make the Cadi copper alloys the ideal material choice for long core pins. Elongation values are listed in Table IV.
Table V :
Mold Alloy | Compressive Yield (ksi) |
---|---|
MOLD-MOR 1 | 80 |
MOLD-MOR 2 | 90 |
MOLD-MOR 3 | 140 |
MOLD-MOR 4 | 155 |
P-20 | 110 |
H-13 | 185 |
420 SS | 215 |
ALUM QC7 | 75 |
Another property important in the selection of the proper mold material is compressive yield strength. These values are given in Table V.
Table VI :
Mold Alloy | Coefficient of Thermal Expansion (10-6/F) |
---|---|
MOLD-MOR 1 | 9.7 |
MOLD-MOR 2 | 9.8 |
MOLD-MOR 3 | 9.7 |
MOLD-MOR 4 | 9.7 |
P-20 | 7.1 |
H-13 | 7.1 |
420 SS | 6.1 |
ALUM QC7 | 12.8 |
Copper alloys have a higher coefficient of thermal expansion than traditional steel mold alloys. On molds or components with long dimension, the rate of thermal expansion must be calculated to ensure proper fit, interference or clearance. Thermal expansion data is listed in Table VI.
Mold-Mor® is a registered trademark of Cadi Company, Inc.
Cadi Copper Alloys meet or exceed industry standards.